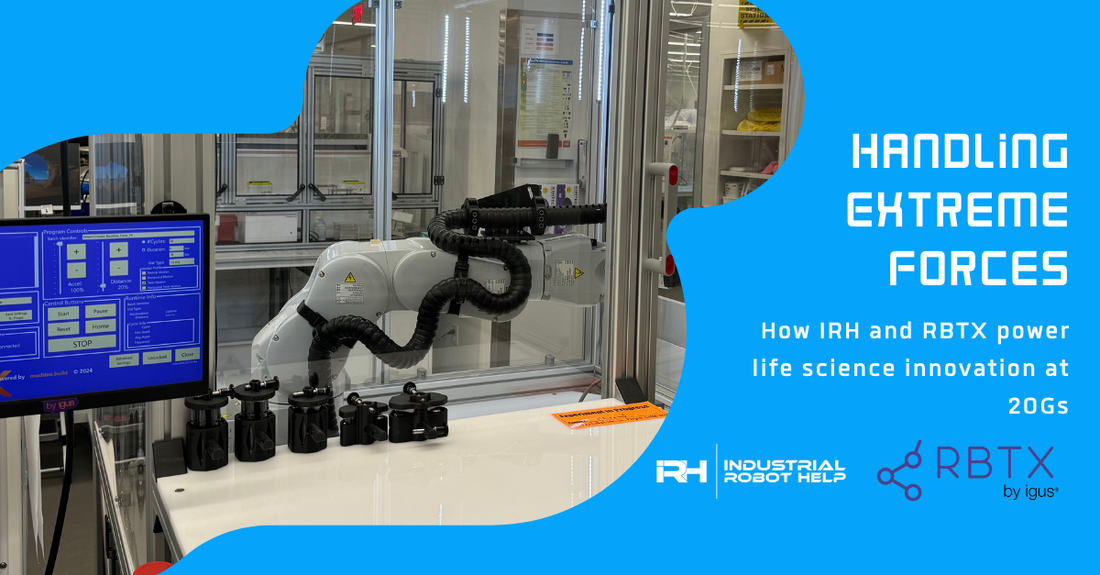
Case Study: Leveraging Creative Engineering and Collaboration to Achieve GSK’s Automation Goals
Share
A Powerful Partnership Bringing Together Key Strengths
The collaboration and eventual partnership between RBTX and Industrial Robot Help (IRH) began at Automate 2023, where IRH founder Willem Oswald and RBTX Product Manager Jan Hennecke first met. According to Willem, there was an instant connection due to the similar mindset of the two. They both have “very creative and strong engineering minds” that “dream big and see way into the future.”
It wasn’t long after this meeting at Automate that IRH became an official partner with RBTX, lending our extensive robotic programming experience to the wide range of products available from the RBTX marketplace. This collaboration has allowed for complete, end-to-end solutions to be developed for RBTX customers, rather than providing just hardware with no integration support.
Automating GSK’s Vial Shaking Process
The project began with the exploration of individual robots and their capacity for acceleration. Given our extensive industry experience, IRH was the ideal partner for RBTX to work with on this project.
IRH was contracted to determine if there was a low-cost yet effective way to automate a manual vial shaking process used to disperse medications in suspension. The process requires vigorous agitation of a pharmaceutical mixture and, to achieve standardized dosing, shaking needs to be consistent across all samples.
An automated solution would relieve the physical stressor to employees and reduce the variability of data caused by the manual process. Beyond keeping the solution low-cost, the customer also required that the machine exert 20 Gs of force to properly disperse suspensions (approximately 4x more Gs than experienced by Formula 1 drivers!).
This requirement initially seemed like an impossible problem to solve given just how extreme 20 Gs of force is. The RBTX and IRH team pushed back slightly on this to see if there was any room for lower forces. GSK held firm, stating they had been able to achieve 20 Gs with manual shaking of an accelerometer. And so, the design team began developing a solution.
Creative Problem Solving with Manual Tests and Robotic Precision
The first low-cost robot tested for this task was an Epson C4, a 6-axis robot arm that boasts impressive speed and flexibility while maintaining a compact size. In the first test, a smartphone with an accelerometer app was zip-tied to the C4, which was programmed to shake the phone as hard as possible — an underwhelming 3Gs.
In the next phase of development the team went back to basics, using their own arms rather than robotic arms to test movement patterns and acceleration generation. Imagine shaking something: for the best results you would use both your elbow joint and wrist joint together, like a whip. Doing so creates more directional change, which results in a larger differential in acceleration while also spreading out the work across multiple joints, thereby limiting strain on a single point in the arm. This whipping motion was capable of achieving the 20Gs the customer required.
Leveraging the principles demonstrated in the manual test, the team transitioned to a larger robot, the Epson C8, and added an extension arm with compliance to more closely simulate the movement created by a human arm when it shakes. This version of the machine was able to mimic flicks of human wrists, elbows, and shoulders while mirroring increased directional change and acceleration differential of a whole arm shaking motion. Tests returned accelerometer readings exceeding the customer requirements of 20Gs.
This rapid, “jerky” movement was unusual for a robot arm, a device typically sought after for high-precision applications and fine movements. This type of out-of-the-box thinking was nothing new for IRH and RBTX, and in fact was a key factor in the development of the final product.
Designing Custom EOAT and HMI Software
With the machine design set, IRH now needed to design custom end-of-arm-tooling (EOAT) that incorporated the compliance and also allowed for a variety of containers to be placed into the system for testing and validation. Usage of 3D printing, an easy choice given igus' and RBTX's experience with both the material development and printing process, enabled IRH to innovate, optimize, and produce the tooling quickly and cost-effectively in-house, reducing production lead time and eliminating the sharing of proprietary information with additional vendors. While no igus 3D printing materials were used for this particular application, in-house printers were utilized to print the final part that was used within the application.
Lastly, IRH built an HMI software with specialized controls (sliders) for directional motion manipulation, motion frequency, and exerted force. The flexibility provided by these operator controls enables the R&D Team to utilize a single robot in the testing of countless medicines, with little to no downtime required to make adjustments to the machine. The HMI code is customizable, allowing for updates based on current testing requirements. The HMI software was developed to be securely installed on the customer’s own hardware utilizing a supplied touchscreen with the robot cell to comply with their IT restrictions.
Meeting Application Requirements Through Low-Cost Automation
Ultimately, the final product was a success and proved to be exactly what the client was looking for. When asked about the design process and the importance of the design team’s flexibility to finding success, Oswald had this to say:
“For us, that shows us that the key points in this whole [mission] are our persistence, or engineering know-how, and then our willingness to be flexible, compliant and helpful to a client instead of taking something we know we can do and trying to solve problems through conventional means.”
Also highlighted as a key point in the project was the low cost of RBTX hardware versus many industrial automation solutions on the market. “Up until a few years ago, there wasn’t anything available for less than $40,000,” said Oswald.
Low-cost automation, as it’s referred to at igus and RBTX, is fundamental to making automation accessible not just to the largest, most well-funded companies, but small and medium-sized businesses that still have to compete with the large industry leaders. In these cases, companies often feel they can’t survive without automation, and are looking for all the help they can get.
If you’re looking to implement low-cost automation in your own application, consider booking a free consultation with Industrial Robot Help!
To learn more about the RBTX marketplace and low-cost automation, visit the RBTX website or take a look at the RBTX white paper.